The city-owned Southeast Community Center (SECC) in Swope Park, Kansas City, Missouri, transformed into a construction site as a new indoor pool was being built. Despite the construction, the facility remained open. To ensure a safe experience for patrons, significant efforts were made to continue programs and services in other areas of the center with minimal disruption.
Waters Edge Aquatic Design designed the pool and provided construction administration services, supporting both the contractor and city staff through coordination efforts. Leading this effort was Trey Bryne, project designer, who was available to the team for frequent job site visits, shop drawing reviews, aquatic related questions, and be the on-site owner’s advocate.
Planning for new construction at a facility that is still open to the public demands well executed coordination efforts. At SECC, coordination planning included executing multiple construction site practices with its staging and amenities, establishing communication channels between the work crew and patrons, and incorporating a unique rock grinding technique to preserve the building.
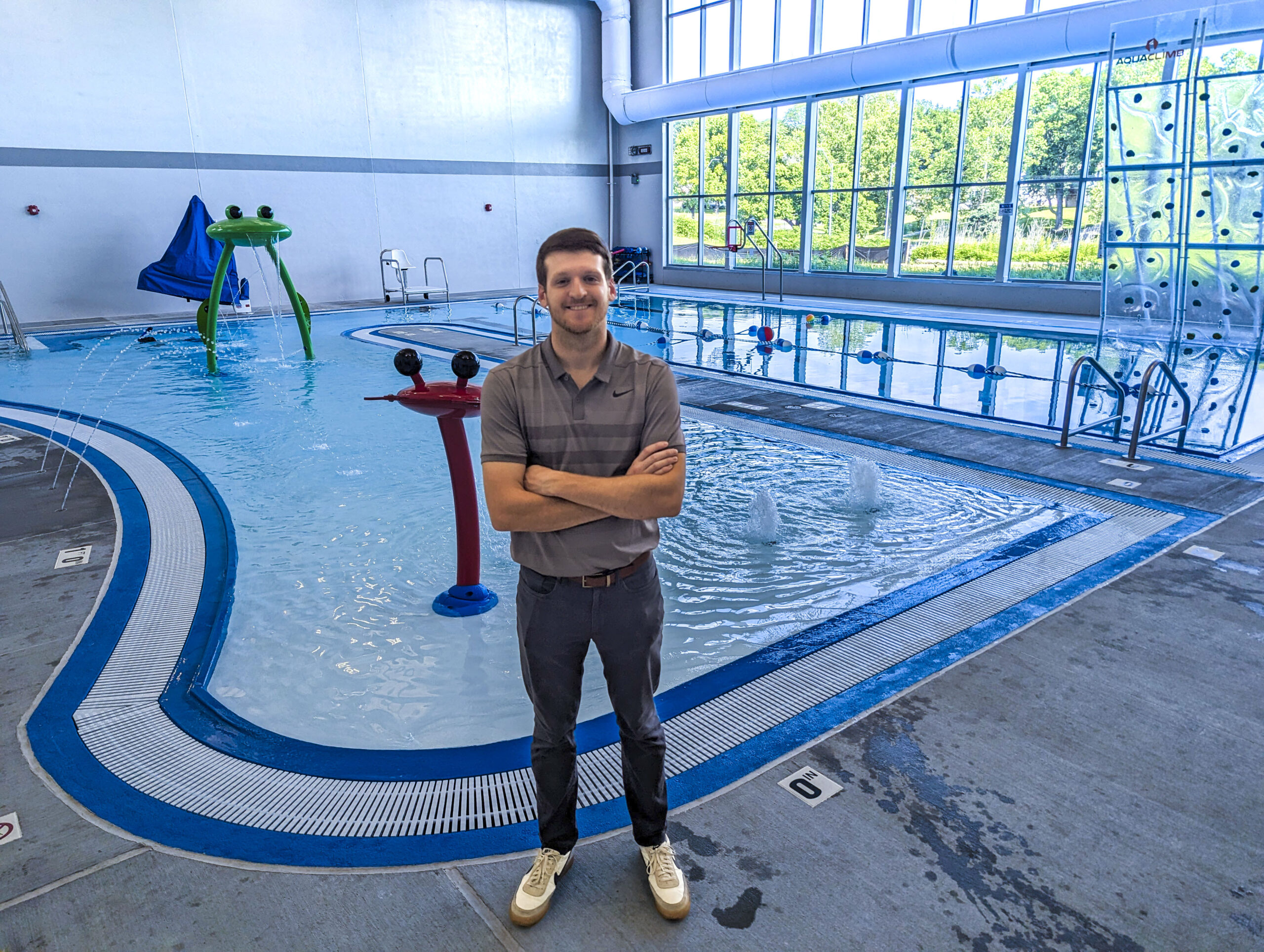
Construction Site Staging
Site management and staging are the first critical areas of focus to minimize patron disturbance. Staging at a construction site involves the coordination on where materials will be stored and delivered, where people can park and access routes, where temporary amenities are located, and other logistical matters necessary for optimizing workflow and safety.
Most patrons at SECC park in an area directly in front of the center’s main entrance. Offset from the regular parking is an overflow lot that is rarely used, which made it a prime staging spot for construction purposes. While the overflow lot was up hill and at the opposite corner of the center than the natatorium space, it still allowed for construction to stay separate from the center’s patron parking.
“To ensure the highest safety standards, we kept all construction activities, including the use of front loaders, trucks, and backhoes, completely separate from the main areas of the center,” said Bryne. “It’s crucial to maintain this separation because an operator’s view can be obstructed, making it unsafe for anyone to be nearby.”
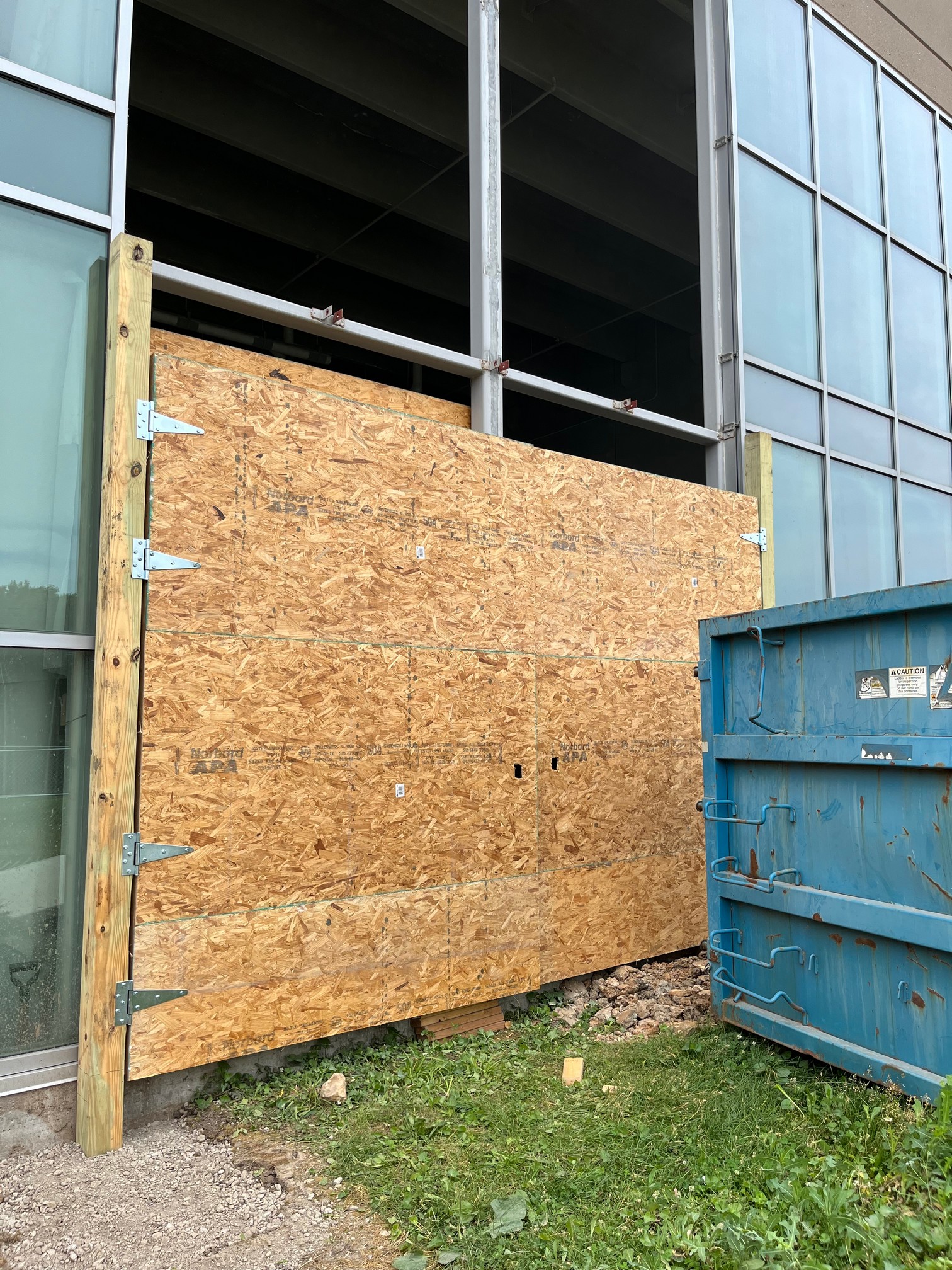
Luckily at SECC, the natatorium has two exterior walls, and one is floor to ceiling glass windows. This allowed the construction crew to have a work area outside of the building next to the pool and away from patrons. A few glass windows were carefully removed, and a temporary access point was created for the large machinery, equipment and materials to enter the building.
“By creating a temporary access point through the natatorium’s exterior, we maintained a secure job site while keeping patrons safe and the center fully operational.”
Temporary Amenities
With construction, there are amenities that may need to be closed off or brought in, such as restrooms and the use of portable bathrooms. With construction happening in the natatorium space, the locker and steam rooms conjoining were closed off. Community center guests were still allowed use of the upstairs restrooms.
“From the start, steam rooms and showers were off-limits, and the center staff communicated in advance the dates for when the entire locker rooms would be closed off,” said Bryne. “This allowed patrons to retrieve their belongings from lockers before it became inaccessible.”
It is important to have signage and communicate this to visitors and members ahead of time so that they are prepared for these types of temporary changes. In addition, their safety is important, and barricades should be used. Temporary walls out of plywood were erected inside the building to keep people out of the construction area.
“To ensure everyone’s safety, the crew built temporary, non-permanent construction doors to lock off sections of the locker room, making them inaccessible even to staff.”
Not only were parts of the locker room closed off, but other access points were closed off as well with temporary structures, which helped to minimize dust, dirt and noise from reaching other parts of the facility.
“With the pool construction involving a large hole for the basin, it was crucial to lock it off to prevent accidents and liability issues, potentially from curious people trying to explore the site and not being aware of the dangers of the hole and equipment.”
Bryne points out that indoor construction, which can be fully secured with locks, requires different protocols compared to outdoor projects that are harder to protect. According to him, “When secure locks are in place, it eliminates the need for the crew to place signage or cover up holes on-site for liability, which is often required in outdoor construction.”
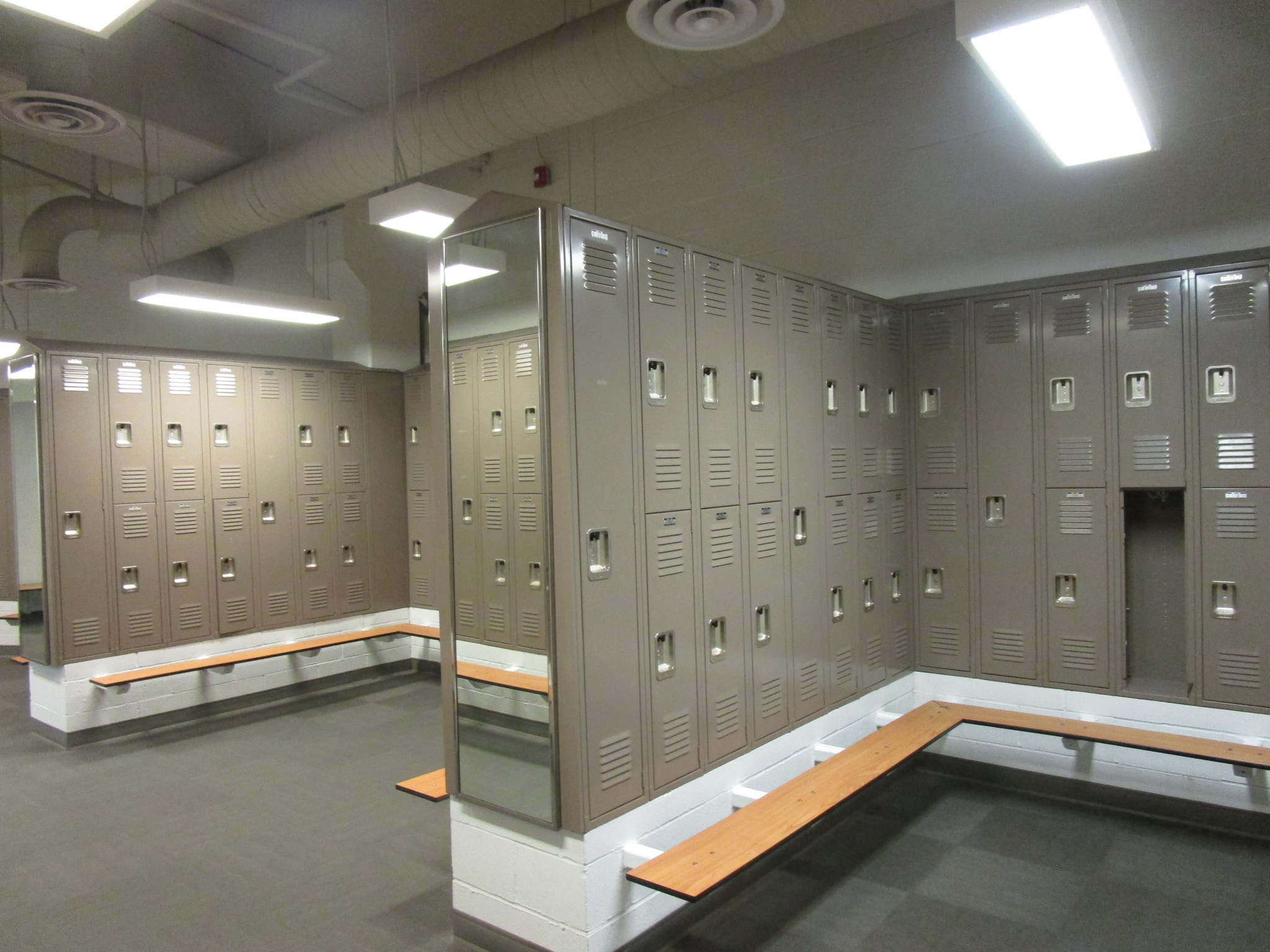
Communication
“Effective communication is key when maintaining a safe construction site, especially with patrons actively utilizing other parts of a building,” stated Bryne. “There becomes an extra layer of attention that is needed.”
At a community center, there are programs that must occur to meet the needs of the community but could be hindered by loud machinery, water being cut off or electricity being turned off.
“Programs such as yoga classes, baby music groups, or sensory play sessions could be disturbed by construction. If there is significant disturbance, then that needs to be communicated through a channel that efficiently links the programs and the construction crew.”
For SECC, there was communication upfront to patrons about the construction. Working hours were communicated and so were times for no hammering. The community center began to count down the days until the pool opened on a visible community board.
“Luckily for SECC, electrical power to the natatorium ran on separate fuses, so power could be shut off as needed for construction without affecting the rest of the building. Only for 30 minutes total was water shut off to the building while it was open, which was communicated to all parties.”
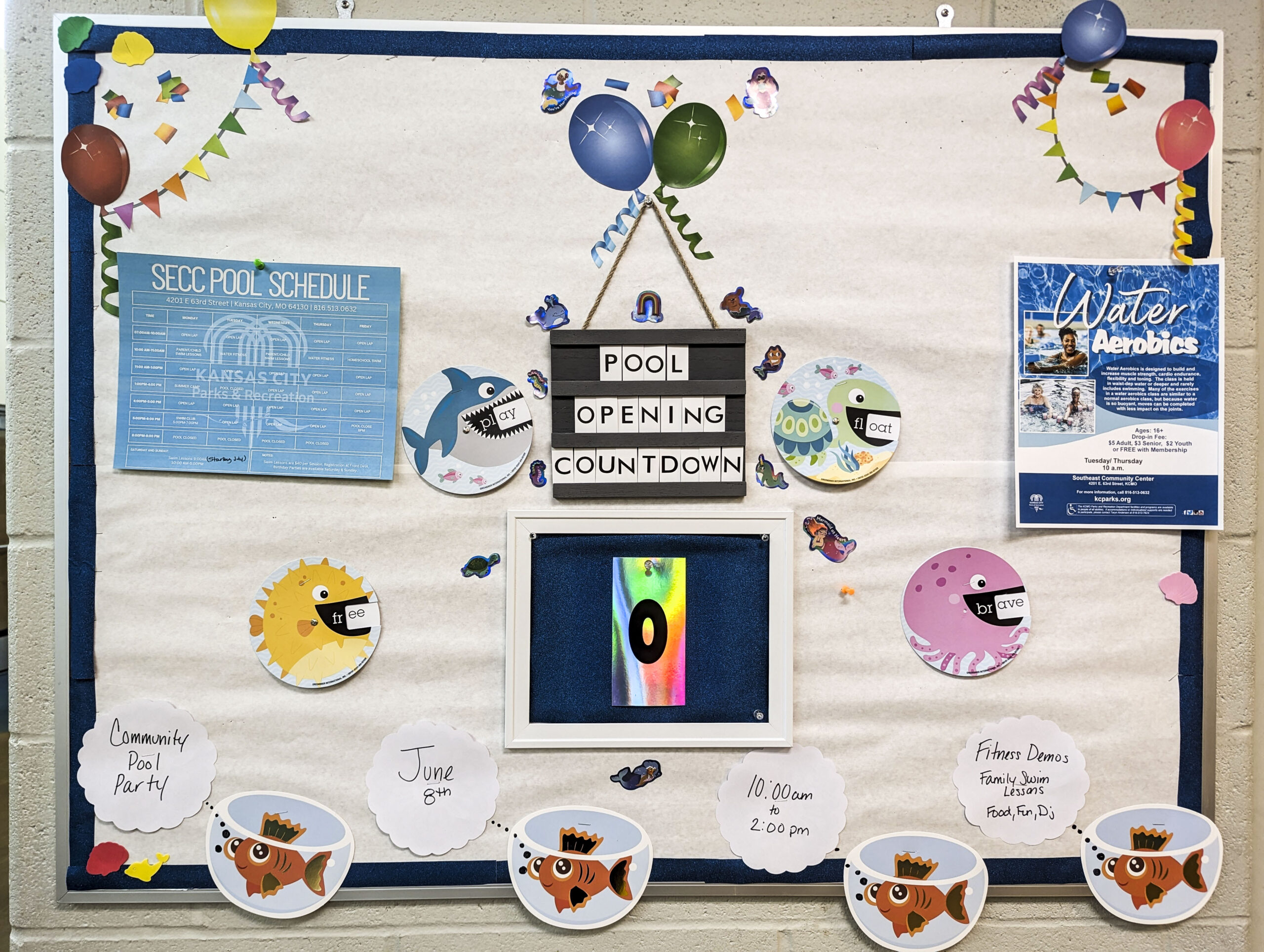
Building Preservation
With the glass walls already present on site, the crew had a challenge to overcome when needing to hammer rock from the ground to dig the pool basin.
“The traditional hammering method would have produced heavy vibrations posing significant risks to the glass walls and the structure of the community center,” said Bryne.
To solve this, rock grinding became the preferred method because it minimized the vibrations.
“A special piece of machinery was brought on site to grind the rock with what could be described as a giant wet saw. This pulverized the rock into finer pieces and prevented the ground from being pounded on.”
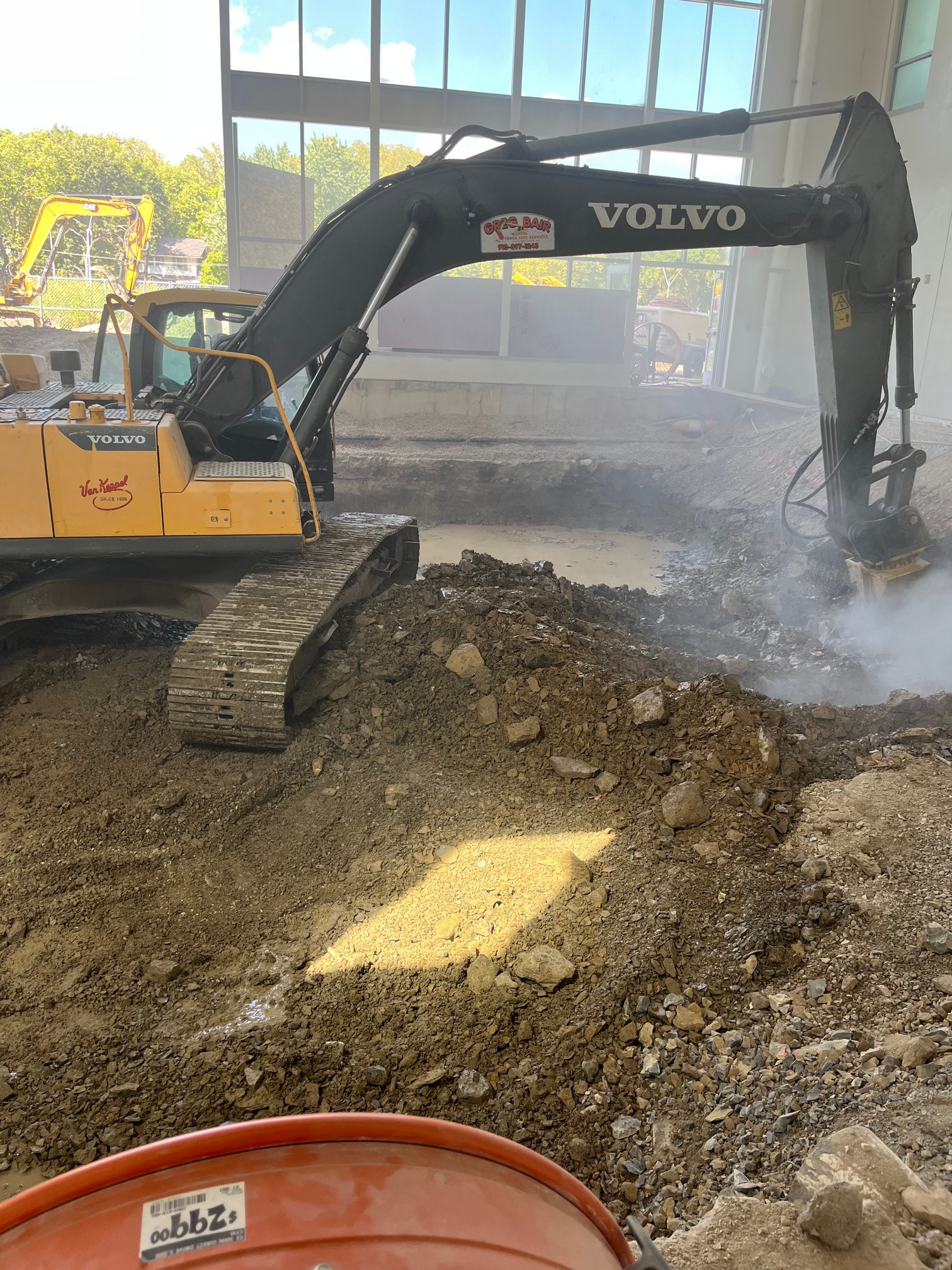
Related Article: Overseeing An Extended Closure
Additional Information
Waters Edge Aquatic Design has the best interests of the client and contractor in mind for the success of the build. Construction administration services are beneficial for all aquatic facility project types but was found to be highly utilized for Kansas City’s indoor pool while keeping the doors open to patrons at the community center. This project serves as an example that a community center, recreational facility, YMCA, fitness center or other indoor buildings can remain open to generate income, while construction of a pool occurs.
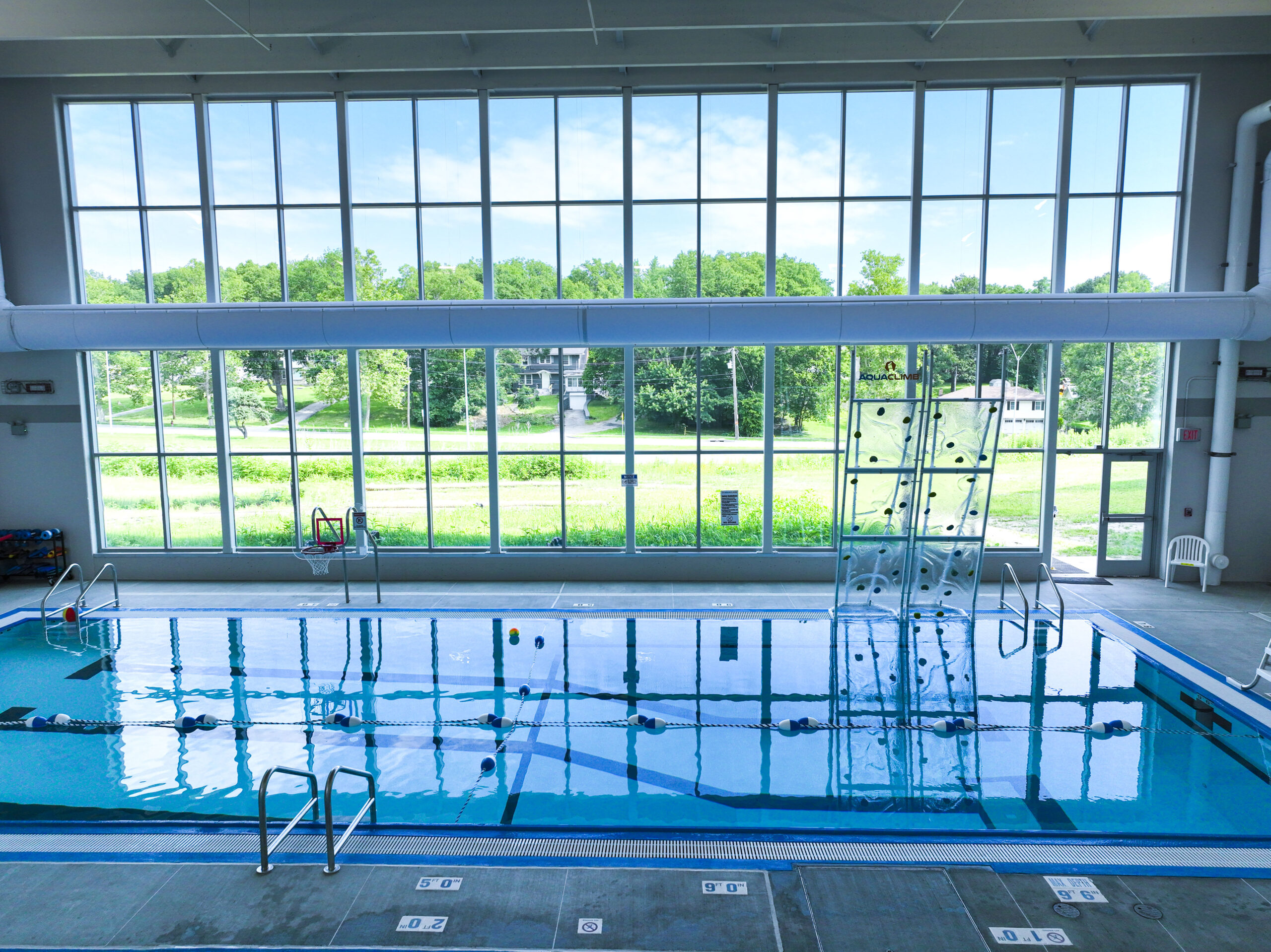